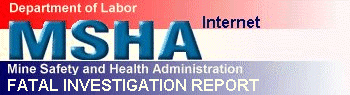
DEPARTMENT OF LABOR
MINE SAFETY AND HEALTH ADMINISTRATION
District 6
ACCIDENT INVESTIGATION REPORT
(UNDERGROUND COAL MINE)
FATAL ROOF FALL ACCIDENT
#1 Mine (ID: 15-17888) Ray-Mac Contracting Inc.
Turkey Creek, Pike County, Kentucky
by
Timothy R. Watkins
Mining Engineer
Larry Little
Coal Mine Safety and Health Specialist
Originating Office-Mine Safety and Health Administration
100 Ratliff Creek Road, Pikeville, Kentucky 41501
Carl E. Boone, II, District Manager
GENERAL INFORMATION
The Ray-Mac Contracting Inc., #1 Mine, MSHA I.D. No. 15-17888, is
located off State Route 612, 0.3 mile from the intersection of
State Routes 612 and 294 at Turkey Creek, Pike County, Kentucky.
The principal officers of the mine are as follows:
Brian Todd Preece.......................................President, Co-Owner
Billy Ray Preece ..........................................Co-Owner
The mine was opened into the Pond Creek coal seam in May 1997, via three drift openings. The mine normally operates 1-1/2 production shifts per day, five days per week. The remainder of the second shift is utilized for maintenance. The 1st shift begins at 7:00 a.m. and continues until 3:00 p.m. The 2nd shift begins at 5:00 p.m. and proceeds until 1:00 a.m.
Approximately 300 tons of coal per day is produced from one conventional mining section at an average mining height of approximately 34 inches. The mechanized mining unit 002-0 (MMU) uses the equipment listed in Table 1 for production. Coal is transported from the face to the section feeder with battery powered scoops. The coal is then transported to the surface via belt conveyors. The section feeder is maintained within two crosscuts of the face.
Each time the belt conveyor is extended a boom hole is
constructed. A boom hole is a cavity blasted in the mine roof to
obtain additional vertical height, to facilitate the extension of
the belt conveyor and the installation of the section feeder.
Equipment Type | Quantity | Manufacturer | Model |
---|---|---|---|
Coal Drill | 1 | SCHROEDER | N/A |
Cutting Machine | 1 | JOY | RB-16 |
Scoops | 4 | S&S | 482 |
Roof Bolting Machine | 1 | FLETCHER | ROOF RANGER |
The last health and safety inspection was completed on June 03, 1998.
DESCRIPTION OF ACCIDENT
On Thursday, August 13, 1998, the second shift crew under the supervision of Chester Dean Harrison, section foreman, began their shift at 5:00 p.m. Three belt splices were made before most of the crew went to the face.
A belt move had been planned for the end of the second shift. In preparation for the upcoming belt move, Harrison and Freddie Allen, roof bolting machine operator, went to the intersection of the last open crosscut and the No. 4 entry to begin work on the boom hole. Allen drilled the holes in the mine roof that were later used to blast the cavity. Roy Dingess, general laborer, assisted Allen in loading the holes. After the holes were loaded, Harrison reportedly used an acetylene and oxygen torch to remove the bolt heads and plates from the roof bolts in the intersection.
At approximately 8:00 p.m., the crew began producing coal. Production from all eight headings continued with coal being hauled through the unsupported intersection, where charged blast holes were present, until approximately 12:00 a.m. At this time coal production ceased and the boom hole was blasted. Harrison and four miners remained on the section to complete the boom hole. Harrison, Roy Dingess and Olen Harris operated the scoops, removing the rock from the intersection. Tommy Blackburn and James Horne, roof bolting machine operators, made preparations to bolt the boom hole.
At 1:15 a.m., Horne heard a rock fall in the vicinity of Harrison. Horne looked and saw the rock on Harrison. He and Blackburn found Harrison in the deck of the scoop with a rock measuring approximately 38" X 60" X 6" lying on top of him. The two men tried, but could not remove the rock. Blackburn summoned Dingess and Harris for help. Horne used a slate bar to raise the rock off Harrison while Blackburn, Dingess, and Harris slid the rock off. Dingess went to get the stretcher while the others removed Harrison from the scoop. Harrison was placed on the stretcher and carried toward the No. 3 entry where he was placed in the bucket of a scoop.
At this time, Billy Ray Preece and Brian Preece (co-owners), who had been notified at home, arrived on the section and performed CPR. Harrison was transported to the surface by scoop. Harrison was pronounced dead at 2:40 a.m., by a Pike County Deputy Coroner.
The Mine Safety and Health Administration (MSHA) was notified of the accident at 2:10 a.m. At approximately 3:45 a.m., personnel from the district office in Pikeville, Kentucky arrived at the mine. Upon arrival they met with company and state officials. A 103 (k) order of withdrawal was issued at 4:30 a.m. Company, State and MSHA personnel proceeded to the 002-0 MMU to begin the underground portion of the investigation.
PHYSICAL FACTORS INVOLVED
The investigation revealed the following factors relevant to the
occurrence of the accident:
General:
- The boom hole was located in the intersection of the last open crosscut and the No. 4 entry.
- The size of the (boom hole) cavity was approximately 2 feet high, 31.8 feet long and 25.75 feet wide. Total height in the boom hole area was approximately 58 inches.
- Boom holes are created every two crosscuts.
- Canopies were not being used on the scoops. Since the mining height (34 inches) was less than 42 inches, canopies were not required.
- Information obtained during the interviews indicated that the practice of going inby permanent roof support was not limited to the creation of the boom holes. Miners stated they had gone inby permanent roof support in the course of the regular mining process.
Boom Hole Construction:
- According to the miners interviewed, all boom holes
were typically constructed:
- Blast holes are drilled approximately two
feet in depth. A hole is drilled next to each roof bolt in the intersection;
- The holes are loaded with explosives and detonators;
- The heads of the roof bolts within the intersection are removed with an oxygen and acetylene torch;
- The area is then blasted;
- Scoops are used to remove the blasted material;
- The area is scaled;
- The protruding roof bolts are cut off with an oxygen and acetylene torch; and
- The intersection is re-bolted.
- Blast holes are drilled approximately two
feet in depth. A hole is drilled next to each roof bolt in the intersection;
- Blast holes were drilled approximately two feet in
depth in the intersection of the last open crosscut and
the No. 4 entry to create a boom hole.
- Sworn testimony indicated upper management at this mine was unaware of the methods used to create a boom hole. According to management, the construction of the boom hole was the responsibility of the section foreman.
Victim:
- According to the miners interviewed, Harrison had been
inby permanent roof support several times during the
process of constructing boom holes.
- When removing the heads of the roof bolts.
- While cleaning up the blasted rock.
- To cut the roof bolts off after the intersection was blasted.
- When removing the heads of the roof bolts.
- Witnesses testified that Harrison told them he did not
want them to go inby permanent roof support. He (Harrison) would go if need be.
- Harrison was cleaning up the blasted material 13 feet inby permanent roof support at the time of the accident.
- The victim was fatally injured when a rock measuring approximately 38" X 60" X 6" fell.
Roof Control:
- Temporary support was not installed in the area.
- Forty-two inch resin roof bolts were being used to
support the roof on the active section.
- Investigators observed twenty-eight roof bolts hanging
at the location of the boom hole. The bolt heads had
been removed with an acetylene and oxygen torch. Testimony
revealed that coal was transported from the face areas through
this unsupported area of roof enroute to the section dumping point
prior to the time of the accident.
- Immediate roof consisted of approximately 5 feet of
shale and the main roof was approximately 50 feet of
sandstone.
- The roof on the active section was found to be in good condition.
CONCLUSION
The accident occurred because the section foreman was working under unsupported roof. Mine management and the miners had become complacent to the hazards of unsupported roof. A practice of working and traveling beneath unsupported roof had been established and continued to the day of the fatal roof fall accident. This practice method required one or more miners to regularly work and travel beneath unsupported roof.
ENFORCEMENT ACTION
Respectively submitted:
Timothy R. Watkins
Mining Engineer
Larry Little
Roof Control Specialist
Approved by:
Carl E. Boone, II
District Manager, CMS&H District 6
Related Fatal Alert Bulletin:
FAB98C19