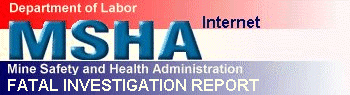
DEPARTMENT OF LABOR
MINE SAFETY AND HEALTH ADMINISTRATION
DISTRICT 7
ACCIDENT INVESTIGATION REPORT
(SURFACE COAL MINE)
FATAL POWERED HAULAGE ACCIDENT
CLOVERFORK MINING AND EXCAVATING, INCORPORATED
KENTUCKY-WEST VIRGINIA STRIP
ID NO. 15-17648
LEONS TRUCKING, CONTRACTOR ID NO. (G4E)
PATHFORK, HARLAN COUNTY, KENTUCKY
AUGUST 19, 1998
BY
ROBERT D. CLAY
AND
STEPHEN W. GARRETT
COAL MINE SAFETY AND HEALTH INSPECTORS
RONALD MEDINA
AND
TERRY MARSHALL
MECHANICAL ENGINEERS
ORIGINATING OFFICE- MINE SAFETY AND HEALTH ADMINISTRATION
HC 66, BOX 1762, BARBOURVILLE, KENTUCKY 40906
JOSEPH W. PAVLOVICH , DISTRICT MANAGER
Report Release Date: January 20, 1999
OVERVIEW
On Wednesday, August 19, 1998, at approximately 2:30 pm, a fatal powered haulage accident occurred at the Cloverfork Mining and Excavating Company Incorporated, Kentucky-West Virginia Strip surface mine entrance haul road located near Pathfork in Harlan County, Kentucky.
Harvey Wilder, age 38, truck driver with fifteen years experience (forty-four weeks of which were at this mine), suffered fatal injuries as a result of the coal truck he was operating overturning on top of him and crushing him between the truck bed and the haulroad surface.
The accident occurred due to the failure of the independent contractor to adequately maintain the subject truck's service braking system.
GENERAL INFORMATION
The Kentucky - West Virginia Strip surface mine is located at Pathfork approximately two miles off of Highway 72 in Harlan County, Kentucky.
The principal officers are:
George Bennett | Superintendent | |
David Partin | Safety Director |
The mine entered operational status on June 1, 1995.
The mine produces approximately 1000 tons of clean coal daily and employs 32 miners on two production shifts, five (5) days per week. Coal is transported by various independent contractors from the mine to the company owned preparation plant located approximately 9.5 miles away.
Cloverfork Mining and Excavating Company, Incorporated, is a wholly owned subsidiary of RB Coal Company, Duane H. Bennett, proprietor.
Leons Trucking is located at Pathfork, Harlan County, Kentucky, and is an independent contractor for Cloverfork Mining and Excavating, Incorporated. Leon Fuson, owner, is involved in directing the daily activities of the company. Three persons are employed by the independent contractor, who work two shifts consisting of a day and evening shift.
The principal officer is:
Leon Fuson | Owner |
The last Mine Safety and Health Administration (MSHA) regular safety and health inspection (AAA) at Cloverfork Mining and Excavating Company, Incorporated was completed on April 13, 1998.
DESCRIPTION OF ACCIDENT
On Wednesday, August 19, 1998, at approximately 6:00 a.m., Harvey Wilder, an independent contractor employee and coal truck driver for Leons Trucking, arrived at the Kentucky-West Virginia surface mine. Wilder was operating a 1971, DM-800 Mack truck, which he had driven from the shop/truck parking lot located at Pathfork, Harlan County, Kentucky. Upon arrival at the mine, he was informed by co-workers that the trucks were to be loaded at the Wallins Coal Pit. At 6:44 a.m., Wilder transported his first load of raw coal to the company-owned preparation plant located approximately 9.5 miles away. He dumped this first load at 7:22 a.m. The shift then proceeded normally and Wilder dumped his second load at 8:56 a.m., a third load at 10:45 a.m., and a fourth load of coal was dumped at 12:47 p.m. as indicated by the weigh tickets from the preparation plant.
Wilder left the preparation plant and returned to the Wallins Pit area. At 1:55 p.m. the end loader operator, Robert Caruso, completed the loading of Wilder's truck. Wilder left the coal pit and had traveled approximately 2.3 miles down the haul road when at approximately 2:30 p.m. he apparently lost control of the truck which overturned onto the mine haul road. The victim apparently either jumped or was thrown from the overturning truck and was crushed between the truck bed and the haul road surface.
At approximately 2:35 p.m., Mike Miracle, a water truck driver for Cloverfork Mining and Excavating, Incorporated, was traveling down the haul road and came upon the accident scene. Scott Brock, a truck driver for B&S trucking, arrived shortly after Miracle. The two walked down to the overturned coal truck and checked the operator's cab. They observed no one in the cab and assumed the driver had caught a ride with someone, since he could not be located.
Moments later, the two observed Wilder under the overturned truck and immediately returned to a vehicle and called for assistance on a citizen's band radio. As a result, co-workers from the Kentucky-West Virginia Strip surface mine site arrived at the scene to assist with recovery efforts.
The Harlan County Emergency Rescue Squad and the Kentucky State Police were immediately notified by Patricia Thompson, a secretary for RB Coal Company at approximately 2:45 p.m.
A front end loader was brought from the Kentucky-West Virginia Strip surface mine site to assist in the recovery efforts. The truck bed was raised slightly and supported with wooden material. The victim was subsequently removed from beneath the truck bed and pronounced dead at 4:00 p.m. by Harlan County Coroner, Phillip Bianchi. Wilders' body was transported by Mountain Emergency Medical Services to the Harlan Appalachian Regional Hospital located approximately 21 miles away in Harlan, Kentucky.
At approximately 3:00 p.m., Patricia Thompson contacted MSHA Headquarters and the Kentucky Department of Mines and Minerals to inform them of the accident. The Headquarters Office immediately notified Edward R. Morgan of MSHA's District 7 Office in Barbourville, Kentucky, who dispatched enforcement personnel to the site.
INVESTIGATION OF ACCIDENT
A 103 (k) order of withdrawal was issued by MSHA inspectors to ensure the health and safety of all persons at the mine until an investigation was conducted. A preliminary examination of the accident scene indicated that an extensive examination of the subject truck would be necessary in order to determine the cause of the accident. A request was made by MSHA for assistance from the Approval and Certification Center in Tridelphia, West Virginia. Ronald Medina and Terry Marshall, mechanical engineers, were dispatched to the accident site to perform the examination of the truck.
After photographs and measurements were obtained, the truck was relocated to facilitate further examination. The truck was towed to the Kentucky State Department of Highway Garage at Loyall, Kentucky. Personnel from Cloverfork Mining and Excavating, Incorporated and Leon Fuson, owner of the truck and president of Leons Trucking, provided a mechanic to assist MSHA's examination.
PHYSICAL FACTORS INVOLVED
The investigation revealed the following relevant physical factors:
- There were no eye witnesses to the accident.
- The subject truck, (Unit No. 21), is a 1971 Mack, model DM-885,
10 wheel tandem haulage truck, Vehicle Identification No. DM885SX2020.
- The truck was overloaded at the time of the accident. It is
estimated that the truck weighed as much as 112,000 pounds,
based upon the maximum weight of previous trips. The
resultant payload of the truck at the time of the accident
is estimated at 78,000 pounds or 167% of the manufacturer's
specified maximum payload of 46,800 pounds. In addition to
overloading the truck's tires and rims, springs and axles,
the estimated payload would have caused the design loads of
the truck's braking system to be exceeded. Mack Truck,
Inc., specified that the truck's brakes primary design basis
involves technical ratings. The Gross Axle Weight Rating
(GAWR) of the front axle is 16,000 pounds and the GAWR of
each of the two rear axles is 32,400 pounds. The combined
GAWR is 80,800 pounds. The brake system was not designed
for an estimated payload or gross vehicle weight (GVW) of
112,000 pounds.
- Evidence at the scene indicated that the truck's right tires
climbed up and over the haulage road berm, traveled 126
feet and overturned onto the haul road surface coming to
rest on the driver side on top of the victim.
- The mine haul road surface at the accident site consisted of
dry, hard packed gravel. The road is approximately 24 feet
wide with an 11 % grade. The haul road generally inclines
for its entire 3.5 mile length and has a sharp turn
approximately 1/4 mile above the accident site. At the
location of the accident the haul road is relatively
straight.
- An examination of the truck cab, after being raised to an
upright position, indicated that the high-low range gear
selector was in neutral and the main gear selector was in
first gear. The engine brake control was found to be in the
"on" position. Due to sustained damage, the truck's engine
could not be operated to permit dynamic tests. The engine
brake was tested by determining whether the engine brake
solenoids received the correct energization voltage. The
solenoid voltage was 11.8 volts when the engine brake was in
the "on" position and a nominal zero volts when in the "off"
position. When either the throttle pedal or clutch was
depressed the voltage fell to a negligible voltage. These
tests indicated no defects with the engine brake control
circuitry which would have rendered it ineffective.
- Along this area of the haul road, reduction to a lower gear,
is a common practice for the purpose of maintaining control
of the speed of the vehicle. The truck drivers interviewed
indicated that the average speed of loaded trucks in the
area where the accident occurred varies from 5 to 10 miles
per hour.
- The actual cab area of the truck sustained only minimal
damage. The windshield was cracked on the left side, but
otherwise no cab glass was broken.
- The following damage apparently resulted from the accident:
the steering axle was separated from the truck; the right
side leaf spring was separated from the frame and the left
side leaf spring was only partially attached to the frame;
the steering linkage was bent and still intact from the
steering wheel to the tires; two power steering lines were
broken; two air lines to the steering axle brake chambers
were broken; one of the lines broke at the brake chamber
fitting and the other at the fitting on the frame; both
breaks were fresh and apparently caused by the accident;
fresh cracks were found on the transmission housing and some
fasteners holding the front case to the bell housing were
broken; the transmission damage appeared to have resulted
from the accident; there was no evidence of any steering
defects other than the damage resulting from the accident.
- Both the throttle and clutch pedal were in the fully
released position and moved without binding when actuated.
No extraneous material was found in the cab to prevent brake
pedal travel.
- The weather was clear and dry at the time of the accident.
- Highway-type coal trucks are not manufactured with rollover
protection (ROPS). A seat belt in proper working condition
was provided but appeared not to be in use at the time of
the accident. The driver's side seat belt had been stored
behind the seat in the truck's cab.
- The accident occurred during the victims fifth trip from the
coal pit to the preparation plant. This was to be the last
scheduled trip of the day. This was confirmed by the weigh
tickets obtained from the company and statements obtained
from co-workers.
- The braking system consists of an air-applied service brake
system, with brakes on each side of the front steering axle and
two rear driving axles. A spring-applied, air-pressure-released
parking brake, integral to the service brakes, is present on both
sides of the two driving axles. The service and spring brake chambers
on the drive axles were all type 30 and the service brake chambers
on the steering axle were type 20.
- The park brake control was found in the "applied" position.
Tests by MSHA revealed that the parking brake would
automatically set when the air pressure fell to approximately 42 psi.
It is not known if the victim had applied the park brake, as it may have
automatically applied subsequent to the accident due to the loss of air pressure.
- The "dry road/slippery road" switch was found in the
"slippery road" position. Tests by MSHA indicated that
the air pressure to the front brake chambers is reduced by
50 % when the switch is in the slippery road position.
- The pushrod travel of each brake chamber was measured. Only
the right forward drive axle's pushrod travel exceeded the
maximum stroke at which brakes need to be adjusted (2 inches
for this type 30 brake chamber). The pushrod travel
measured 2 7/16 inches at approximately 100 psi. The
mounting bracket holding the left-front brake chamber was
broken as a result of the accident. Therefore this pushrod
travel could not be measured.
- The left-front brake drum wear surface and brake linings
were coated with grease and dirt. The source of the grease
was overflow from the "s-cam" and anchor lube fittings.
Grease was apparently deposited on the linings whenever
these fittings were lubricated during routine maintenance.
As a result, no significant braking force was generated by
this brake.
- The right front brake drum diameter exceeded the maximum
wear tolerance by 0.240 inches. The brake linings and drum
were also coated with grease and dirt from the "s-cam" and
anchor lube fitting overflow. One of the four lining
segments was broken, with a portion missing. No significant
braking force was generated by this brake.
- The left-forward drive axle's brake drum exceeded the
maximum wear allowance by 0.280 inches. One of four lining
segments was broken, with a portion missing, exposing two
fastening devices.
- The left-rearward drive axle's drum diameter exceeded the
maximum wear allowance by 0.190 inches.
- The right-rearward drive axle's drum diameter exceeded the
maximum wear allowance by 0.270 inches.
- The right-forward drive axle's drum diameter exceeded the
maximum wear allowance by 0.325 inches. Four fastening
devices holding one of the two lining segments of the brake
shoe were broken off and the entire lining segment was
loose. A set screw was missing from the "s-cam" linkage
which allowed the roller to shift. This created an offset
between the "s-cam" and the roller such that only one half
of the "s-cam" was riding on the roller surface. The
pushrod travel of the brake chamber exceeded the maximum
stroke which brakes need to be adjusted (2 7/16 inch stroke
was measured with a maximum of 2 inches allowed). No
significant braking force was generated by this brake.
- Prior to raising the truck to an upright position, the air
system was pressurized to approximately 100 psi using a
portable air compressor. Air leakage was audible at the
right-rearward drive axle brake chamber and an intermittent
leak was heard from the hand valve exhaust hose that
terminates on the engine side of the firewall.
- During an air leakage test prescribed by Mack Truck, Inc.,
with the engine "off" and the service brakes "released",
the air pressure drop measured approximately 5.5 psi per
minute. The air pressure drop should not have exceeded 2.0
psi per minute. Further tests were conducted after the
truck was turned upright. The pressure drop with the engine
"off" and the service and parking brakes "released"
increased to 13.5 psi per minute, this exceeded the 2.0 psi
per minute allowed by Mack Truck, Inc., specifications.
With the engine "off", service brake "applied" and parking
brake "released", the pressure drop was measured at
approximately 11.5 psi per minute. According to Mack Truck,
Inc., specifications, the pressure drop should not have
exceeded 3.0 psi per minute in this case, with the service
brake "applied".
- The air tank drain petcocks were opened and water was
ejected as well as viscous black slurry.
- The independent contractor, Leons Trucking, operates 3
(three) trucks. Leon Fuson, owner, stated that he
personally performed repairs and maintenance on all three
trucks. Fuson maintained intermittent maintenance and
repair records on the subject truck involved in the
accident. No pre-operational vehicle inspection report was
provided or available on the subject truck on the date of
the accident. (No record is required unless equipment
defects effecting safety are found).
- The victim held a class "A" commercial drivers license and
had approximately fifteen (15) years experience as a truck
driver prior to the accident.
- The victim received his commercial driver's license on
February 28, 1996, to operate a truck of this type on public
roadways. A portion of the trip from the coal pit to the
preparation plant and return was on public roadways.
- The victim's training records consisted of annual refresher, task training and hazard training provided for several different mine locations. However, neither the operator, Cloverfork Mining and Excavating Incorporated, or the independent contractor, Leons Trucking, could provide records of the required hazard training for the Kentucky-West Virginia Strip mine, I.D. No. 15-17648.
CONCLUSION
The accident occurred due to the overloading of the subject truck in conjunction with the 11% grade, causing the vehicle to exceed the normal operating speed, which was not minimized due to the independent contractor's failure to adequately maintain the truck's service braking system.
ENFORCEMENT ACTIONS
The following citations and orders were issued during the accident investigation.
- A 103 (k) order no. 4864050, was issued to ensure the safety
of all persons at the mine until the investigation was conducted.
- A 104 (a) citation no. 7457864 was issued to the independent
contractor for failure to adequately maintain the truck's
braking system and for exceeding the manufacturer's maximum
payload specifications.
- A 104 (a) citation no. 7457187 was issued to the mine
operator for failure to provide required hazard training for
the victim.
- A 104 (a) citation no. 7457875 was issued to the contractor for failure to provide required hazard training for the victim.
Submitted by:
Robert D. Clay
Mine Safety and Health
Inspector/Accident Investigator
Stephen W. Garrett
Mine Safety and Health
Inspector/Surface
Ronald Medina
Mine Safety and Health
Mechanical Engineer
Terry Marshall
Mine Safety and Health
Mechanical Engineer
Approved by:
John M. Pyles
Assistant District Manager
for Enforcement, District 7
Joseph W. Paplovich
District Manager, District 7
Related Fatal Alert Bulletin:
FAB98C20