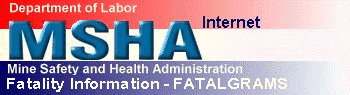
DEPARTMENT OF LABOR
MINE SAFETY AND HEALTH ADMINISTRATION
DISTRICT 7
ACCIDENT INVESTIGATION REPORT
(Underground Coal Mine)
Fatal Machinery Accident
Mine #16
Manalapan Mining Co. Inc.
I.D No. 15-17811
Highsplint, Harlan County, Kentucky
August 15, 2000
by
Billy A. Parrott
Coal Mine Safety and Health Inspector
Barbourville, Kentucky
Originating Office-Mine Safety and Health Administration
HC 66 Box 1699, Barbourville, Ky 40906
Joseph W. Pavlovich, District Manager
Report Release Date: February 8, 2001
OVERVIEW
At approximately 1:15 p.m. on Tuesday, August 15, 2000, a fatal machinery accident occurred on the 002 working section of the Manalapan Mining Co. Inc., Mine # 16, near Highsplint, Harlan County, Kentucky. Bruce Perkins, a 40 year old continuous mining machine operator with 22 years experience, suffered fatal injuries when he was caught between a Model 14CM10 Joy continuous mining machine and the coal rib. Mining had been completed in the No.1 working place and the continuous mining machine was being moved across the working section to the No.5 working place. While moving the trailing cable in order to prevent it from being damaged, Perkins and Brad Hopkins, a shuttlecar operator who was helping Perkins, were positioned between the continuous mining machine and the coal rib. Based upon the statement of Hopkins the continuous mining machine suddenly turned, resulting in both men being caught between the coal rib and the machine.
The accident occurred as result of the mine operator's failure to insure that all persons were outside the turning radius and pinch points of the continuous mining machine while the machine was being operated, as required by the approved roof control plan.
General Information
The Mine # 16, located near Highsplint, Kentucky, is operated by Manalapan Mining Co. Inc. The mine employs 27 persons underground and 8 persons on the surface. The mine is opened by four drift openings into the Wallins coal seam which averages 48 inches in thickness. The mine produces coal one shift per day five days per week on two sections. Maintenance and service work are performed on the second shift.
The mine produces an average of 2000 tons of raw coal daily. Coal is transported from the face utilizing two Joy Model 21SC shuttlecars. The roof is supported during advance mining using a Eimco dual head roof bolting machine equipped with an Automated Temporary Roof Support (ATRS) system. Currently the mine consists of two working sections, main entries, panels, and gob areas created by pillar extraction. The land is owned in fee by Manalapan Land Company.
The principal officers of the operation are as follows:
Duane H. Bennett ............... Chief Executive OfficerThe last Mine Safety and Health Administration (MSHA) regular Safety and Health Inspection (AAA) was completed on 6/15/2000.
George Bennett ............... Vice President
Richard Scruggs ............... Treasurer
Richard D. Cohelia ............... Safety Director
DESCRIPTION OF THE ACCIDENT
The day shift of the 002 working section started at 6:00 a.m., as scheduled, on August 15, 2000, under the direction of Ronnie Penny, Section Foreman. Mining proceeded at normal production through the day. Production had begun in the No.5 heading. After completing the mining cycle in the No. 1 heading at approximately 1:00 p.m. the Joy continuous mining machine was backed down the No. 1 entry. A shuttlecar was used to pull slack in the trailing cable from across the section back down an adjacent entry. Bruce Perkins, continuous mining machine operator, assisted by Brad Hopkins, shuttlecar operator, was in the process of relocating the continuous mining machine to the No.5 heading. Perkins had trammed the continuous mining machine to the crosscut between the No.2 and No.3 entries. A twin head Eimco Model 5310-40 roof bolting machine was located in the No.2 heading and its trailing cable was hung along the inby rib of the crosscut between No. 2 and No.3 entries. In an attempt to keep the continuous mining machine from contacting the roof bolting machine's trailing cable, the continuous mining machine was positioned approximately three feet from the outby coal rib. Based upon statements made in interviews, Perkins asked Hopkins to assist him in preventing the continuous mining machine's trailing cable from being caught by the track.. The cable's position between the coal rib and the continuous mining machine resulted in Perkins and Hopkins being positioned between the continuous mining machine and the coal rib. Interview statements indicated that as the miners worked, the continuous mining machine suddenly started and pivoted on its tracks, pinning Perkins and Hopkins against the coal rib.
David Helton, roof bolting machine operator, was working nearby in the No.2 heading. Based on statements obtained in interviews, his roof bolting machine was to be moved to the No.1 entry after the continuous mining machine moved across the section. Helton stated that he heard Hopkins call for help and that he proceeded immediately to provide assistance. Hopkins, stated that, at this point, he was unable to reach the radio remote control box which was located in front of Perkins. Helton stated that he crawled beneath the rear corner of the continuous mining machine and was able to retrieve the radio remote control unit. He then used the control unit to pivot the continuous mining machine, freeing the two miners. Helton stated that he had to "wiggle" the connector plug on top of the unit's battery in order to energize the remote control system.
Ronnie Penny, section foreman, was reportedly working in the No.5 entry when he heard calls for help. Arriving on the scene, Penny, also a Mine Emergency Technician, found Perkins lying on the mine floor. At this time Hopkins, who was uninjured, rose and went to retrieve the first aid kit. Penny stated that he immediately checked Perkins for vital signs and found a pulse and shallow breathing. Perkins was next placed into the bucket end of a scoop and transported to the track. Statements obtained during interviews indicate that while enroute to the track, Perkins' pulse had become weaker. Upon the victim's arrival at the track, Penny immediately administered Cardio Pulmonary Resuscitation (CPR), before transferring the victim to a waiting, rail mounted, personnel carrier. Due to low clearance, CPR was not continued for the short trip to the surface. Upon his arrival on the surface, Perkins was examined by Tom Lunsford of the mine operator's safety department. Lunsford stated that he found no vital signs and again resumed CPR.
Perkins was subsequently transferred by Mountain EMS Ambulance Service to the nearby Cloverfork Clinic. At 2:32 p.m. Perkins was officially pronounced dead. An autopsy revealed that the victim died as a result of "cardiac contusions and lacerations due to blunt impact of the trunk with visceral and skeletal injuries."
INVESTIGATION OF ACCIDENT
At approximately 1:30 p.m. on August 15, 2000, Elmer Thomas, Coal Mine Safety and Health (CMS&H) Inspector, arrived on the surface on the Manalapan Mining Company, Inc. Mine # 16 just as Perkins was being transported to the surface. Thomas immediately notified Dan Johnson, (CMS&H) Inspector, at MSHA 's Harlan, Ky, field office. Johnson dispatched Dennis Bryant, CMS&H inspector to the mine. Johnson notified John Pyles, District 7 Assistant District Manager for Enforcement, at his office in Barbourville Ky. An Accident Investigation Team consisting of Billy Parrott; CMS&H Inspector, Jim Langley, Supervisory CMS&H Inspector, Dennis Cotton, Mining Engineer, and Foster Brock CMS&H Specialist-Electrical, was dispatched to the mine to begin the investigation.
Mine Safety and Health Administration (MSHA) and Kentucky Department of Mines and Minerals (KDMM) jointly conducted the investigation with the assistance of mine management and the miners. Formal interviews were conducted in conjunction with KDMM on August 16, 2000. Seven interviews were conducted. None of those interviewed requested that their statements be kept confidential.
On August 17, 2000, Robert Boring, Electrical Engineer, of MSHA's Approval and Certification Center assisted in the on-site investigation and the subsequent testing and evaluation of the continuous mining machine and associated components. On site, after replacing the discharged battery on the remote control unit, all functions of the remote control system were tested. The covers of the main controllers were then removed and the internal components and associated wiring were examined for signs of problems which could result in unexpected machine movement (See Appendix B). All components and associated wiring checked on this day were found to be functioning properly.
During the investigation, components of the continuous mining machine's radio remote control system were collected and taken for evaluation at MSHA's Approval and Certification Center in Triadelphia, West Virginia. The results of this evaluation are discussed further in this report.
A list of those who were present and/or participated in the investigation is included. (See Appendix A).
DISCUSSION
Interviews were conducted with mine personnel who were determined to potentially have information related to the accident. Based upon statements from the interviews the continuous mining machine in use at the time of the accident had a previous history of operational problems related to the radio remote control unit. (See Appendix B) This continuous mining machine had been in use at the subject mine for approximately three weeks prior to the accident. Statements indicate no mechanical problems were experienced with the continuous mining machine on that shift.
An in-depth investigation was conducted at MSHA's Approval and Certification Center to determine if the radio remote control system and all related machine components were functioning properly. Testing of the remote control system's Remote Control Multiplexer, Radio Transmitter, RF Receiver, and Demultiplexer Control Panel showed that all functioned properly.
No unintentional start-up of any function of the continuous mining machine was experienced during any of the onsite or later testing of the machine component's configuration. The previously reported malfunctioning of the radio remote control system was evaluated by the investigators and no evidence was found that the malfunctioning of the radio remote control system or any related machine components contributed to the fatality. Cross activation of the continuous mining machine by other radio sources was ruled out as the 001 Section continuous mining machine was located approximately 6,500 feet away.
PHYSICAL FACTORS INVOLVED
The following physical factors were determined to be relevant to the occurrence of the accident:
1. The accident occurred underground on the 002 MMU at Manalapan Mining Co. Inc's. Mine # 16, MSHA I.D. No. 15-17811.
2. Mining height in the area where the accident occurred is approximately 50 inches.
3. The mine floor in the area where the accident occurred was very wet and muddy.
4. The continuous mining machine was located approximately two feet from the coal rib when the accident occurred.
5. There were no other remote control system units or other RF signals present on the 002 section. The 001 section is located approximately 6,500 feet away.
6. A Joy model 14CM10, 950 VAC, 3-Phase, 60 Hz, continuous mining machine, Serial No. JM 4997 was in use on the 002 section.
7. The remote control system used on the continuous mining machine consisted of the following components: Matric Limited Model 205-376 Remote Control Multiplexer, P/N 601843-172, S/N 26012N010, MSHA IA 460; Matric Limited Model 500-256 (318 MHz) Permissible Radio Transmitter, P/N 601843-136, S/N 25611N18, MSHA Approval 9B-170-1; Matric Limited Model 500-255 (318 MHz) Cavity RF Receiver, P/N 601843-0135, S/N 25509K14, MSHA IA-461-1; Matric Limited Model 500-200 Demultiplexer Control Panel, P/A 603238-0001, S/N 68308AA007, MSHA IA-457. All the listed components were tested by MSHA's Approval and Certification Center, Division of Electrical Safety. All components were found to be functioning properly.
CONCLUSIONS
The accident occurred as result of the mine operator's failure to insure that all persons were outside the turning radius and pinch points of the continuous mining machine while the machine was being operated, as required by the approved roof control plan.
ENFORCEMENT ACTIONS
1. A 103 (k) Order, No. 7461893, was issued to insure the safety of the miners until an investigation could be conducted.
2. A 104 (a) Citation, No.7498414, was issued for violation of Title 30, Part 75.220(a), stating, in part, that the mine operator was not complying with the approved Roof Control Plan. Two miners were caught between the radio remote controlled continuous mining machine and the coal rib. The plan requires, in part, that "the continuous mining machine operator and all other persons must be outside of the machine's turning radius and away from the pinch points."
Related Fatal Alert Bulletin:
APPENDIX A
List of persons furnishing information and or present during the investigation.
Manalapan Mining Company, Inc. - Officials
David Patterson ............... Mine SuperintendentManalapan Mining Company, Inc - Employees
Doug Lunsford ............... General Mine Foreman
Richard D. Cohelia ............... Safety Director
Tom Lunsford ............... Safety Department
Ronnie Penny ............... Section Foreman
Brad Hopkins ............... Shuttlecar OperatorKentucky Department of Mines and Minerals
David Helton ............... Roof Bolting Machine Operator
Denny Creech ............... Roof Bolting Machine Operator
William Ball ............... Supplyman
Tracy Stumbo ............... Chief Accident InvestigatorMine Safety and Health Administration
Ronnie Hampton ............... Inspector, Accident Investigator
George Johnson ............... Inspector, Accident Investigator
Davit Hoskins ............... Inspector, Accident Investigator
David Disney ............... Supervisor
Jim Langley ............... Supervisory CHS&H InspectorManufacturer's Representatives
Billy A. Parrott ............... CHS&H Inspector/Accident Investigator
Dennis J. Cotton ............... Mining Engineer/Accident Investigator
Foster Brock, Jr. ............... CHS&H Inspector/Electrical Specialist
Dennis Bryant ............... CHS&H Inspector
Elmer Thomas ............... CHS&H Inspector
Gary Harris ............... CHS&H Special Investigator
Robert Boring ............... Electrical Engineer, Electrical Safety Division Approval and Certification Division
Thomas Grooms ............... Attorney-Office of the Solicitor
Dave Thomas ............... Joy-Certification Engineer
Kevin DeLaney ............... Matric- Manager, Service Support
Dave Ghrist ............... Matric-Service Support Team Leader
Wally Coxen ............... Matric-Engineering Manager